house zero: designed and printed by lake | flato and icon
architecture practice lake | flato and construction technologies company ICON have teamed up to realize the 3D printed ‘house zero’ — a project that is as fascinating as it is beautiful. located along a corner lot in a suburban neighborhood just outside downtown austin, texas, the house stands out at once with its undulating forms and unique ribbed texture, all blended together with a mid-century modern expression.
the house took just under two weeks to print, its walls made with a proprietary cementitious-based material, ‘lavacrete,’ insulation, and steel for reinforcing. this system replaces a traditional building system that involves multiple steps, saving time, waste and cost. the 2,000-square-foot, three-bedroom, 2.5-bath home even sits alongside a 350-square-foot, one-bedroom, one-bath accessory dwelling unit. designed for net-zero energy, the climate-responsive house is truly a demonstration of what living could be like.
the ‘tree wall’ mimics the organic forms of tree trunks | image © casey dunn
balancing hard and soft
the collaboration between ICON and lake | flato resulted in a ‘house zero’ whose high-tech processes introduce a material and atmosphere that feel warm and natural. the layers of lavacrete squish onto themselves in a way that is just slightly irregular enough to suggest a natural occurrence. houses built of concrete can sometimes feel cold. the interiors of house zero by lake | flato balance out ICON’s lavacrete with the introduction of warm timber, and finally, soft textiles which complement the ribs and undulations.
the 3D printed ‘house zero’ is a place that invites exploration. from the rippling ‘wiggle wall’ in the master bedroom, to the smallest detail where hardwood meets soft lavacrete, the space is filled with moments of discovery at every scale.
after visiting house zero, designboom spoke with melodie yashar, director of building design and performance at ICON (see here) along with architect and associate partner lewis mcneel of lake | flato (see here).
the timber roof appears to float lightly over the house | image © casey dunn
dialogue with icon
DB: could you explain how the fabrication process informed the design of the architecture?
melodie yashar (MY): absolutely. our hardware system, our construction system, always impacts and influences the way that design happens. architecture, to me, really informs the way that we introduce hardware changes and how we’ve informed like hardware requirements. basically, we have a large scale, gantry-based 3D printer that deposits a proprietary material that we’ve developed known as ‘lavacrete.’ layer by layer, we use that system to 3D print the building.
we work within the constraints of the width of the gantry printer. when we collaborate with architects and designers external to ICON, we look for new ways to actually push forward the technology, push the envelope, and think differently about how we can design wall systems in the future.
view of the living area and the office nook beyond | image © casey dunn
DB: what is the difference between the ‘lavacrete’ and regular concrete? I recall discussing that regular concrete would have flattened in on itself unlike the lavacrete.
MY: part of the reason why we have a proprietary material is to allow the flow ability of the material, the rheology of the material, to actually extrude from the pump in real time. and so the properties of the material have to be such that when it lands, it sets and it has a different cure time than traditional concrete. that’s why we’ve developed a material that’s specific to our system and for 3D printing. it’s a mortar-based concrete. not exactly like a traditional concrete, but it’s specific to allow for flow ability through the machine to be deposited.
view from the entrance into the round dining nook | image © casey dunn
DB: what are the benefits of 3D printing a house over a more typical construction method? what can be achieved through 3D printing that wouldn’t be possible any other way?
MY: unlike traditional kind of building methods with steel and with wood, we have an innately digital design to construction process where basically, designers and architects can bring a 3D model to us can design virtual name three dimensional in digitally in three dimensions. and then we have a process that actually takes that model and converts it into the toolpath, and the G-code for the dirt.
it’s a very different way of designing and developing design documents for construction. and we see it as one way of sort of modernizing the way that architecture is approached in the future in the way that construction can step up one level higher to get closer to a true building information modeling workflow.
the ‘wiggle wall’ in the master bedroom | image © casey dunn
DB: what did the construction documents look like? it must be a hybrid of a G-code, and a typical floor plan?
MY: we have a proprietary kind of generative BIM program, and which is basically an algorithm that develops the G-code for our wall system. and how we approach it depends on who we’re working with. some architects and designers are more accepting of this new way of working with us and collaborating. others are less.
so we have early adopters, and there will be late adopters. but if if we don’t have an opportunity to be as collaborative on g code coordination as we would like, we sort of approach it from the traditional shop drying process, which is that we produce drawings, the architect checks them and then those are the ones issued for construction.
image © designboom
DB: how was it collaborating with lake | flato?
MY: they were extremely excited and extremely interested in upping the ante on what’s possible and what we’ve built to date when it comes to construction, 3D printing. so the ‘wiggle wall’ and a lot of the curved forms that you see within the house surface things that have never really been done in residential construction before, there’s lots of videos and examples online of how either 3D printing providers or in lab settings or research settings, you have these beautiful ornate forms.
this is the first time where it’s really within house and permitted building that can be occupied and sold in the future. so I see that is a really exceptional aspect of the project. and lake | flato was with us every step of the way.
image © designboom
DB: I was really struck by that ‘wiggle wall’ and also the ‘tree wall,’ those undulating bays in the living space. can you explain the process of designing those forms? why incorporate curves?
MY: the truth of the matter is that it is a really expressive element of the wall system that you can’t achieve using traditional cast in place concrete, or wood siding methods. so you get this wonderful plan light and texture with these undulating forms that you won’t otherwise get unless you have a very extensive computational design-build process. in that case, everything is custom manufactured for this one element.
but because we’re 3D printing, we’re able to print that wall just like any other. so that was a key advantage and a key opportunity that we saw to really become expressive in the design. and lake | flato, of course, was able to leverage that and can use it as part of the design language that they adopted for the design in the house.
image © designboom
DB: I recall the stepping vaults of your mars dune habitat — what are the limitations when designing in section? are these domed spaces something that you will push more in the future?
MY: we definitely want to be thinking ahead to how we can create vaulted forms and dome shapes that would basically consider the entire building enclosure for a house. it’s a challenge in construction, and 3D printing overall, and it’s not something that anyone has solved. we’re yet not capable — without other support mechanisms — to print horizontally and create these really cantilevering forms, but it’s something that we’re interested in.
and we definitely see applications for that in the future. we are looking at other ways of printing groups similar to the mars dune alpha project, and then installing those afterwards.
image © designboom
DB: austin is quite a temperate climate. how would this house perform in colder climates or maybe even more urban contexts?
MY: when we’re considering the performance of the wall system and and the assembly itself, I wouldn’t say that we have limitations when it comes to climate zones are where we want to build. it’s actually an extremely efficient system in that it maintains a lot of thermal mass. so that leads to great energy savings. but beyond that, it’s an R-20 wall so we can work in colder climates. we don’t really see an issue in building in rural areas versus urban areas, and eventually we definitely want to be thinking about building in other climate zones apart from where we are right now.
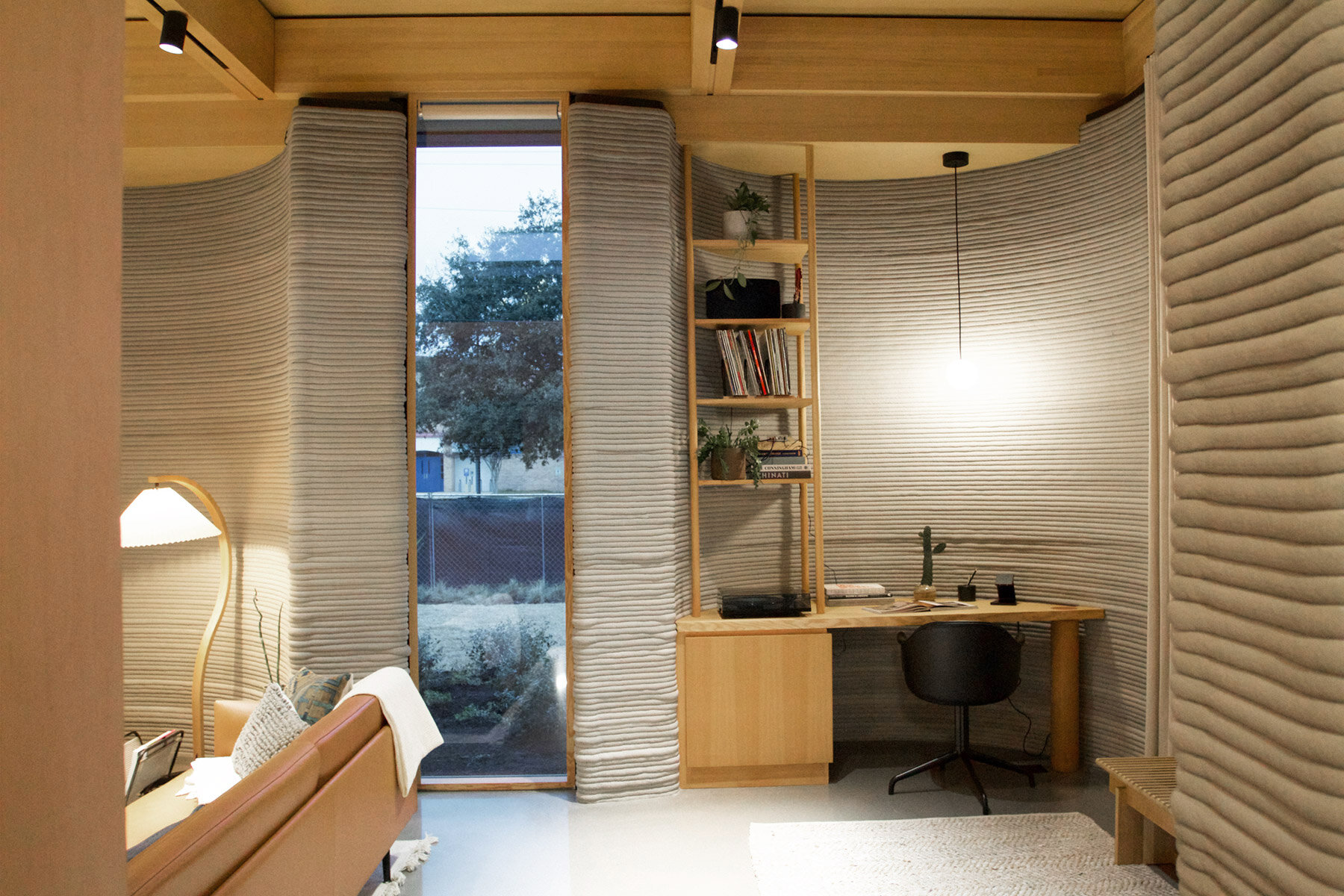
DB: could you describe what the wall section looks like?
MY: sure, we print in what are known as ‘beads.’ an individual bead is an individual printed layer. we have two adjacent structural beads that are on the interior side, and then a veneer bead on the exterior. the veneer bead is the one which tends to be the most performative. so it can introduce all of those wiggle walls and tree walls and beautiful undulating forms that become expressive for for the architecture and for the geometry. that’s basically how the wall assembly works, we have two interior beads, and then a veneer bead on the outside.
image © designboom
DB: how have the designs of these houses developed since the earliest versions? are there any lessons that you’ve learned along the way?
MY: absolutely. every project we have, we take it as an opportunity to iterate and improve on our design to build and construction process, in addition to our material as well and our hardware, so we’re always iterating and always improving to introduce a more reliable and more efficient system. as far as the design goes, we have iterated quite a bit on the wall assembly itself. and depending on various applications, like for resilient housing in areas that are more hurricane prone, or that might be subject to like in impacts from the outside.
in hurricane prone areas, we have a different wall in some way than what we’re looking at for production scale housing, which maybe would not need as robust and durable of a wall system. so we look at how we can introduce efficiencies, depending on the application and the project. and separate from that, will we always iterate to improve the performance of our system.
image © designboom
dialogue with lake | flato
DB: can you describe the collaboration with ICON creating house zero? what was the role of your team at lake | flato?
lewis mcneel (LM): our job was to produce the most stunning house we possibly could to showcase, ICON’s technology. gratefully, ICON gave us a huge amount of freedom to think about what a house of the future could look like, and specifically how a printed house could transform the way houses are thought about — both to design them and to live in. so we presented an initial concept that we pretty much did on our own. with it, we had a heavy amount of dialogue back and forth with ICON from a technical standpoint about where they were at with their technology, and what it can handle.
image © designboom
we got just one specific request from jason ballard — other than to make the most beautiful house in the world — the other funny specific request was to have a round room somewhere. and we understood the reason for that. this process is specifically good at curves and things you may not be able to normally do with stud framing.
we don’t normally get to do curves and round rooms and we would shy away from them, depending on the material that we’re working with. but we knew right away, we got that vision like, ‘okay, well, you want to round room, we’ll give you a round room’ (laughs). so we found a way to elegantly incorporate a round dining room, and we even squeezed in a round bathroom experience. that was the only real constraints ICON gave us.
so we produced the concept design, and produced some renderings, and they all seemed to love it. then we just moved ahead and detailed it, documented it, and got the thing built — and it ended up exactly the way we rendered it! that was huge, just watching how ICON themselves built the vision that we designed for them. they executed it beautifully. and it was a pretty painless process in that regard. we just produced a concept, they said ‘move ahead,’ and we did, and that was it!
image © designboom
DB: is there any part of the process that was surprisingly easy?
LM: the easy part was showcasing such a beautiful material. lake | flato always wants to get to know really deeply the construction processes that we’re working with, whatever they are. whether it’s a steel process for the building, or a masonry out in a hill country site, or this groundbreaking new robotically controlled process, it’s all the same to us. we want to learn exactly how to how to leverage its specific advantages. having some early meetings with ICON to understand the potential — structure, envelope, wires — all the ways to use printed concrete.
we quickly developed a set form and functional ideas for how we can implement this material in an honest way inside a lake | flato house so that it wouldn’t feel like lake | flato suddenly trying to adapt some strange, alien thing into our world. so we got to use a groundbreaking new material and celebrate its beauty. but that took the same brains that we always use in our all of our projects. it’s simply revealing and expressing its unique character, and not fighting against what it can’t do.
image © designboom
DB: and any challenges?
LM: the challenge was that we did the concept work amazingly, without knowing exactly what the site was going to be. and we guessed pretty close, we knew it was a corner site. but once we got the actual site, ICON and we were all surprised by a few of the setback requirements. so we had to exhaustively begin scooching squishing things down a tiny bit further, to sit within some previous cover limits that the site had, and to fit with some utility easements and some driveway access requirements. you might notice the driveway comes in at a fun, swoopy angle off the street and doesn’t square the building.
the driveway entry point had to be a certain distance away from the street corner, which we couldn’t have predicted when we started. instead of rearranging the whole house, we decided to just deform a concrete wall and allow that angled driveway. it was a beautiful way to take a problem that a site presented and show the plasticity of this material and how well it can squish to take on a number problems and overcome them in an easy way.
if we had been building a blocky, rectilinear house and suddenly had to insert a strange angle driveway, the material would not have responded well and would have messed with the whole feel and look of the house. instead we did it, and it even helped celebrate the material all the more.
image © designboom
DB: can you speak about the integrated wood cabinetry? concrete can sometimes seem very cold, but your interiors were very warm. I also noticed a lot of details with the carpentry were the wood was cut with custom curves to fit against the 3D printed layers.
LM: yes, and thanks for noticing all the fun details. when you look closely, you catch a variety of strategies we were trying out. when a piece of hard wood hits a bumpy concrete texture, you have two options: you can scribe the wood, or you can notch into the concrete. and actually the house successfully tries both. so there is a little bit of experimenting going on. but we had to be thoughtful, and that’s what lake | flato does over and over, discovering how to join two dissimilar materials in an elegant way. this is just another problem that we would have encountered with a rusticated stone wall.
we had a very specific rule for ourselves about the wood, which was to not try anything beyond rectilinear, straight stuff involving wood. we wanted the concrete to shine as the sinuous, curvy experience and to show a clear diagram of a concrete, or a lavacrete, curving shell with very simple wood boxes that can be set inside. the hope is that one day you could print a big chunk of the house and simply drop in some boxes at another point. then you’ve got yourself a warm wooden house with the wonderful materiality of the wood alongside the surprising warmth of lavacrete.
image © designboom
DB: working in the digital space, how did you combine the two materials when drawing and modeling? how did the G-code and the revit model come together as one?
LM: it’s the same process as working through a shop drawing process with a fabricator. for a normal project, architects would draw millwork drawings for a cabinet. that’s their best guess, or their best desire for what it would look like. then those drawings get sent to a fabrication shop, which then redraws everything exactly the way they know it would need to be built.
here, ICON was the contractor and fabricator for this part. so we drew a pretty elaborate slab plan that meticulously documented all the slab conditions. ICON took that file and worked with it and implemented it on site in the same way that a subcontractor fabricator would produce any piece. so there were shop drawings, and there were digital models that we built to make sure everything was right.
image © designboom
DB: when you were designing these curving walls, especially the tree wall, what initially informed the development of the geometries or curves themselves?
LM: the rippling texture of that tree wall on the outside was actually developed hand in hand with lake | flato and ICON software engineers. we all wanted to use a few key moments to celebrate how printed concrete could shift not just in plan, but a little bit in section too. these flare-outs make the house feel rooted, sort of like a tree. but they’re also just an honest celebration of what amazing stuff this material can do. so lake | flato defined the general look of that experience, and we worked a lot with ICON software engineers and robotics people to translate that into a principal code.
image © designboom
DB: are there any more details that you wanted to share about the house?
the project resulted in a fully lake | flato house through and through using this amazing ICON technology. ICON graciously let us provide all the interior design and finish of the house as well. we’re super proud that it’s not just the ‘hard architecture’ that is lake | flato through and through, but so is the beautiful finish out experience. we get to do that on just a handful of projects, but we really got to do that here. when you see this house, you’re seeing our full vision for what life can be like.
3D printing (766)
architecture in texas (66)
architecture in the US (1507)
architecture interviews (267)
carbon neutrality? (152)
dbinstagram (2250)
ICON (13)
lake flato (6)
residential architecture and interiors (3981)
PRODUCT LIBRARY
a diverse digital database that acts as a valuable guide in gaining insight and information about a product directly from the manufacturer, and serves as a rich reference point in developing a project or scheme.