a new way to build
pioneering a technology platform, new york-based company assembly OSM kicks off the ‘post-modular’ era of building delivery. conceptualized by bill and chris sharples, co-founders of SHoP architects, the company worked in close collaboration with advisors from boeing, spaceX, and tesla. this multidisciplinary team seeks to modulate the process of mid-to-high-rise building construction so that it becomes safer, faster, and more efficient.
this week, assembly OSM unveils its first one-bedroom unit built using revolutionary digital design technology combined with advanced manufacturing techniques. assembly OSM’s innovative building delivery methodology is powered by a sophisticated technology platform that re-thinks the entire process to eliminate human error, resulting in significantly reduced project timelines and achieving true cost certainty. as the team embarks on its delivery phase, it aims to translate the platform into its first full-scale apartment building in new york.
visualization of a future project in new york | images courtesy of assembly OSM
architecture becomes automated
when designboom visited the company‘s factory in new jersey, assembly OSM noted its DNA from SHoP architects. born out of 25 years of expertise on the SHoP side, they have learned how the architects turn design into design for fabrication. the team has also taken advantage of the expertise offered from boeing, spaceX, and tesla, and inserted their methods of manufacturing and managing supply chain into its processes.
assembly OSM has picked up on the advancements from the aerospace and automotive industries and brought them to the building world which, as they note, is certainly behind the curve in terms of how automated-technologically driven it is.
visualization of a future project in new york
in conversation with the team
in front of a holographic, interactive 3D model of a modular apartment unit, assembly OSM describes its process.
assembly OSM (AOSM): our whole model is based off of a supply chain. we manage the digital model, ‘the platform,’ we develop the building designs from our building generator, we develop high fidelity fabrication drawings that get pushed into our supply chain, and things like this come back. so this is an example of our MEP systems, that they come to our facility.
‘assembly is the name of the company, but it’s also our methodology. these get assembled in our site and moving things clip into place. we’re pushing a lot of that construction down into the ecosystem in our tier two and tier three suppliers. what we’re seeing here is a fully fit out bathroom pod with piping, toilet, and tub coming from a tier two facility, coming to a facility like this at tier one, and getting clipped into place. then our mechanical system goes in, then flooring, closets.
‘what’s really interesting is the mechanical system. it normally involves a lot of complex, labor-intensive construction — tape, joints, drain pipes — now all of that is happening at a different facility then ours downstream. much more like the way that cars and airplanes are put together than buildings. so if you look at a toyota camry, for example, the dashboard of the car is made by a different supplier. it is fully functional with the steering wheel, the radio, the ductwork, when it comes to toyota. their role is designing it, ensuring quality control, and then assembling it into the final product. we play a very similar role in the building ecosystem, managing the process from a technological perspective, doing that final assembly, and then stacking it on site.
exploded visualization of one module
designboom (DB): can this system adapt to more complex floor plans or layouts?
AOSM: two points on that — we’re starting with 15 to 30 stories, not an easy product to master. using that as the basis for developing our systems is probably the right starting point because our platform is agnostic to the structural system and the region. so we can plug and play, we have the flexibility for growth. we’re using steel chassis here, but for example we can swap that for a CLT structural system.
in terms of ensuring that the engineers have everything checked out, our digital model is completed to the point where every screw and every piece of tape in this is modeled in… that’s how we get this level of accuracy and really locking in cost certainty.

factory sequence drawing
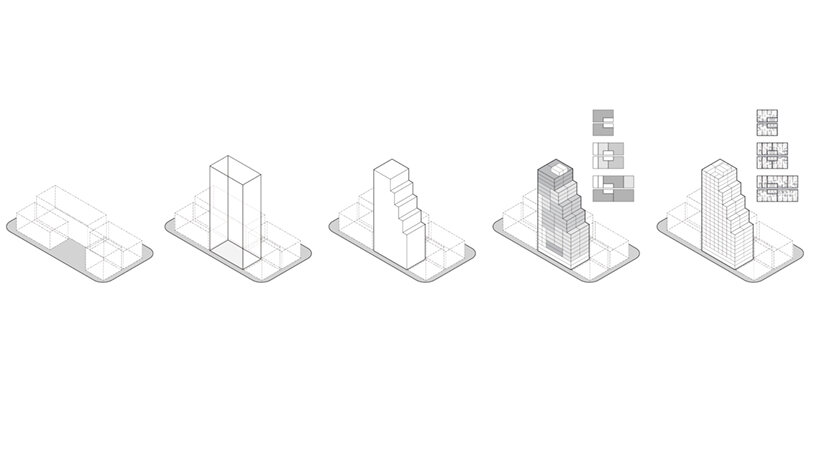
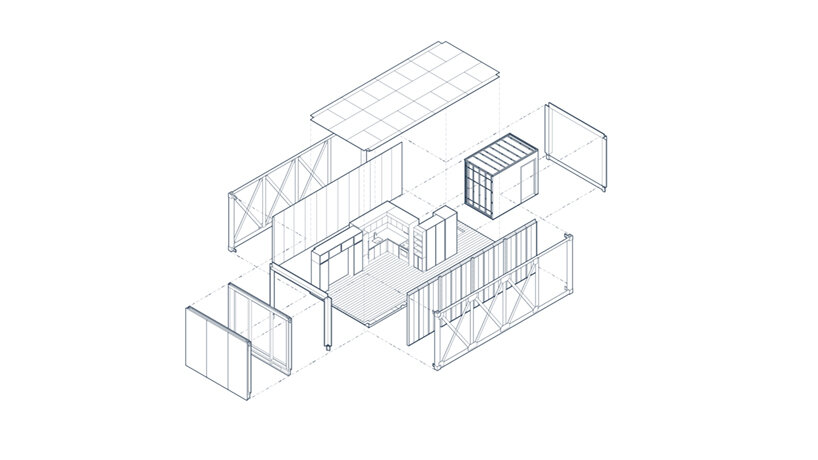
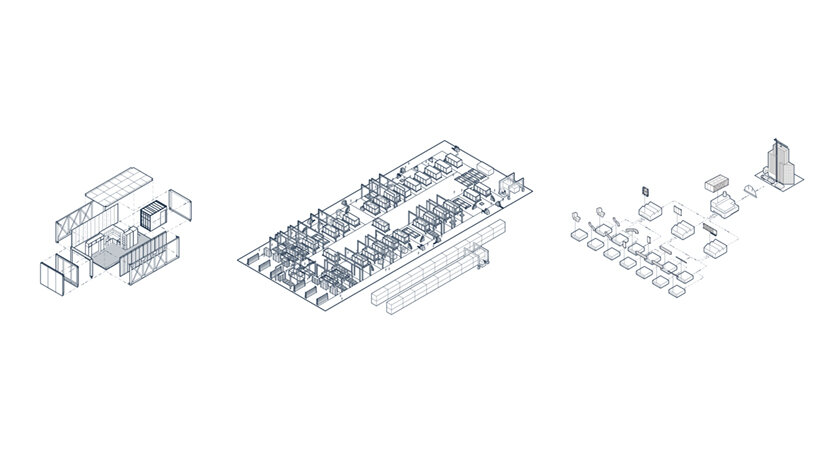
DB: it also overcomes human error during installation, yes?
AOSM: yes, exactly. if you think about traditional construction, you have a sophisticated architect working in 3D software, and they print to PDF 2D drawings and hand that off to the contractor. then the contractor rebuilds the 3D model in their coordination phase. so that handoff introduces tons of human error, just on the design and information sharing standpoint.
then when you actually get to the physical construction, there’s this whole element of inferred scope in traditional architecture and construction where you’re not modeling out the four screws that go into every hinge — but we have that. there’s no ambiguity in terms of what our suppliers have to deliver, which allows us to have a much tighter quality control. and we hold them to quality control standards in our facility. when it arrives at our facility we have quality control, and then when it gets stacked on site, we have quality control again. and because we have that high fidelity down to the screw, we can check things at really high precision.
interior tour of a newly completed prototype unit
DB: do you expect that this will mark a step toward more affordable housing?
AOSM: right now we’re targeting market rate, new york products. that’s our starting point, that’s where we have a lot of experience. but when you think about the development of the supplier ecosystem, you’re going to be able to deliver much faster, much cheaper, innovate on different product offerings, different price points. the unit we have behind us is like the rolls royce. but our platform is agnostic to that. we can dial it up or down depending on what the developer wants, what the market needs, the region, all of that.
interior of a newly completed prototype unit
DB: construction is quickly becoming more automated. can you speak about this system’s role in that trend?
one hundred percent. from the perspective of jobs, it’s going to be key where we unlock pipeline. there’s a massive housing crisis. everyone knows we need more housing. but how do you do it? assembly is one of those ways, and it’s one of the truly scalable models that we have. when you’re building more, you have more jobs. the other side of that is the environment and the ecosystem that we’re developing. we’re not just developing on-site construction jobs, which is a small part of what we do, we’re developing an ecosystem of suppliers. they can work in controlled environments on the ground — they’re not up on the ladder, they’re not in the crane.
that opens up a wider potential worker pool which can tap into different communities. it can level a lot of the playing field and open up an opportunity for different groups to participate in construction that have been you know, either not willing or able because of how inefficient and dangerous it is. that’s a huge opportunity that we have to help move the needle on.
interior of a newly completed prototype unit
interior of a newly completed prototype unit
architecture in new york (587)
prefabricated homes and buildings (201)
residential architecture and interiors (3981)
SHoP architects (38)
spaceX (44)
tesla (88)
PRODUCT LIBRARY
a diverse digital database that acts as a valuable guide in gaining insight and information about a product directly from the manufacturer, and serves as a rich reference point in developing a project or scheme.